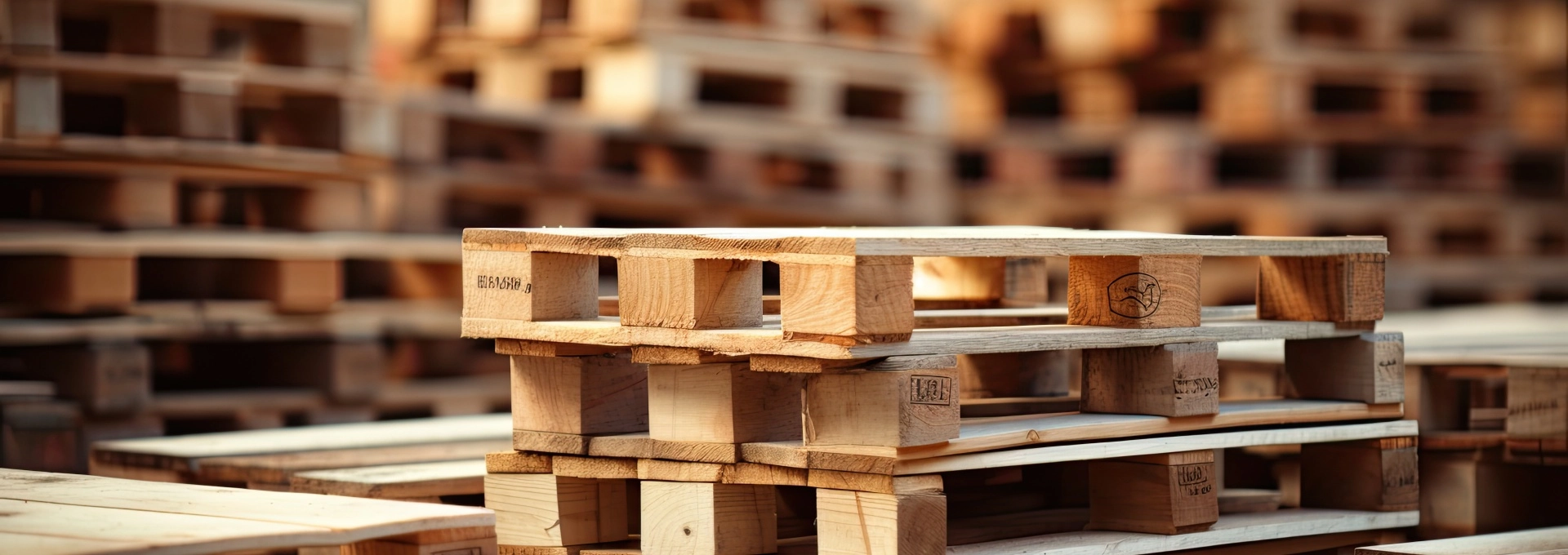
La gestion efficace du stockage de palettes représente un défi majeur pour de nombreuses entreprises à Dijon. Avec l'augmentation des coûts immobiliers et la nécessité d'optimiser chaque mètre carré disponible, il est crucial d'adopter des stratégies intelligentes pour maximiser l'espace de stockage. Une organisation réfléchie peut non seulement améliorer la productivité, mais aussi réduire les coûts opérationnels et minimiser les risques de sécurité. Découvrez les meilleures pratiques pour optimiser le stockage palette à Dijon et transformer votre entrepôt en un espace de travail plus efficace et rentable.
Optimiser l'organisation des palettes dans votre entrepôt
L'organisation judicieuse des palettes dans votre entrepôt est la pierre angulaire d'une gestion efficace de l'espace. Une disposition bien pensée peut augmenter considérablement la capacité de stockage tout en facilitant l'accès aux marchandises. Selon une étude récente, une réorganisation intelligente peut augmenter la capacité de stockage jusqu'à 30% sans nécessiter d'agrandissement physique de l'entrepôt.
Définir des zones de stockage spécifiques
La création de zones de stockage dédiées est essentielle pour une gestion optimale de l'espace. Commencez par analyser vos flux de produits et identifiez les articles à forte, moyenne et faible rotation. Organisez ensuite votre entrepôt en conséquence, en plaçant les produits à forte rotation près des zones d'expédition pour réduire les distances de déplacement. Cette approche peut réduire les temps de préparation des commandes de 20 à 30%.
Considérez également la mise en place d'une zone tampon pour gérer les fluctuations saisonnières ou les pics d'activité. Cette flexibilité vous permettra de vous adapter rapidement aux changements de demande sans perturber l'organisation globale de votre entrepôt.
Utiliser des racks de rangement adaptés
Le choix des racks de rangement appropriés est crucial pour maximiser l'espace vertical de votre entrepôt. Les racks à palettes traditionnels sont efficaces, mais pour certains types de produits, des solutions plus spécialisées peuvent offrir une meilleure utilisation de l'espace. Par exemple, les racks à accumulation peuvent augmenter la densité de stockage jusqu'à 75% pour les produits homogènes à forte rotation.
Pour les articles de petite taille ou à rotation rapide, envisagez l'utilisation de systèmes de stockage dynamique. Ces systèmes utilisent la gravité pour faire avancer les palettes, réduisant ainsi les temps de préparation et maximisant l'utilisation de l'espace.
Mettre en place un système de rotation
La mise en œuvre d'un système de rotation efficace est essentielle pour optimiser l'utilisation de l'espace et minimiser les pertes dues à l'obsolescence des stocks. Les deux principales méthodes sont le FIFO (First In, First Out) et le LIFO (Last In, First Out). Le choix entre ces deux méthodes dépendra de la nature de vos produits et de vos besoins opérationnels.
Le FIFO est particulièrement adapté aux produits périssables ou sujets à l'obsolescence, tandis que le LIFO peut être plus approprié pour les produits non périssables ou dans certaines situations fiscales. Une étude a montré que l'application correcte d'un système de rotation peut réduire les pertes de stock de 15 à 20%.
Choisir le matériel de manutention approprié
Le choix du matériel de manutention adéquat est crucial pour maximiser l'efficacité de votre stockage de palettes. Un équipement bien adapté peut non seulement augmenter la productivité, mais aussi améliorer la sécurité et réduire les dommages aux marchandises. En fonction de la configuration de votre entrepôt et de la nature de vos produits, plusieurs options s'offrent à vous.
Les chariots élévateurs traditionnels restent un choix populaire pour leur polyvalence. Cependant, pour les allées étroites, les chariots à mât rétractable peuvent offrir une meilleure manœuvrabilité tout en permettant d'atteindre des hauteurs plus élevées. Pour les entrepôts avec des plafonds très hauts, les transstockeurs automatisés peuvent être une option intéressante, offrant une utilisation maximale de l'espace vertical.
N'oubliez pas de considérer l'ergonomie du matériel pour vos opérateurs. Des équipements ergonomiques peuvent réduire la fatigue et les blessures, augmentant ainsi la productivité à long terme. Par exemple, les transpalettes électriques peuvent réduire considérablement l'effort physique requis pour déplacer des charges lourdes.
Investir dans du matériel de qualité peut sembler coûteux au départ, mais cela peut se traduire par des économies significatives à long terme. Une étude récente a montré que l'utilisation d'équipements de manutention adaptés peut augmenter la productivité de 20 à 30% tout en réduisant les dommages aux marchandises de 10 à 15%.
Tenir compte des normes de sécurité
La sécurité est primordiale dans tout environnement de stockage de palettes. Non seulement elle protège vos employés et vos marchandises, mais elle contribue également à l'efficacité globale de vos opérations. Les normes de sécurité ne doivent jamais être considérées comme un frein à la productivité, mais plutôt comme un moyen d'optimiser vos processus.
Commencez par vous assurer que tous vos équipements de stockage, tels que les racks et les palettes, sont conformes aux normes en vigueur. En France, la norme NF EN 15635 régit l'installation et l'utilisation des systèmes de stockage en acier. Un respect strict de ces normes peut réduire les risques d'accidents de 40 à 50%.
Mettez en place un programme régulier d'inspection et de maintenance de vos équipements. Les dommages non détectés sur les racks peuvent non seulement compromettre la sécurité, mais aussi réduire la capacité de stockage effective. Des inspections régulières peuvent prévenir jusqu'à 70% des défaillances potentielles des équipements.
Formez régulièrement votre personnel aux bonnes pratiques de sécurité. Cela inclut non seulement la manipulation correcte des équipements, mais aussi la reconnaissance et le signalement des risques potentiels. Une étude a montré qu'un programme de formation complet en sécurité peut réduire les accidents du travail de 30 à 40%.
Mettre en place un système de gestion informatisé
L'implémentation d'un système de gestion d'entrepôt (WMS - Warehouse Management System) est devenue incontournable pour optimiser le stockage de palettes. Un WMS efficace peut transformer radicalement vos opérations, offrant une visibilité en temps réel sur vos stocks et améliorant la précision de vos inventaires.
Un bon WMS vous permet de suivre chaque palette depuis son entrée dans l'entrepôt jusqu'à sa sortie. Cette traçabilité accrue peut réduire les erreurs de picking de 70 à 80%, améliorant ainsi la satisfaction client et réduisant les coûts liés aux retours et aux réexpéditions.
De plus, un WMS avancé peut optimiser l'utilisation de l'espace en suggérant les meilleurs emplacements pour chaque palette en fonction de divers critères tels que la taille, le poids, la fréquence de rotation et les compatibilités de produits. Cette optimisation peut augmenter l'utilisation de l'espace de stockage de 10 à 20%.
Intégrez votre WMS avec des technologies complémentaires pour maximiser son efficacité. Par exemple, l'utilisation de scanners portables ou de systèmes de reconnaissance vocale peut accélérer les processus de picking et réduire les erreurs. Certaines entreprises ont rapporté une augmentation de la productivité de 25 à 35% grâce à ces technologies.
N'oubliez pas que le succès d'un WMS dépend en grande partie de la qualité des données qu'il contient. Mettez en place des procédures rigoureuses pour assurer l'exactitude et la mise à jour régulière des données de votre inventaire. Une base de données précise est essentielle pour une planification efficace et une prise de décision éclairée.
Former le personnel aux bonnes pratiques de stockage
La formation du personnel est un élément crucial dans l'optimisation du stockage de palettes. Même les systèmes les plus sophistiqués ne peuvent être pleinement efficaces sans des opérateurs bien formés pour les utiliser. Un programme de formation complet peut non seulement améliorer l'efficacité opérationnelle, mais aussi réduire les risques d'accidents et de dommages aux marchandises.
Commencez par une formation approfondie sur les principes de base du stockage de palettes. Cela devrait inclure la compréhension des différents types de palettes, les techniques de chargement sécuritaire, et les meilleures pratiques pour l'utilisation des équipements de manutention. Une étude récente a montré que les employés bien formés aux techniques de base peuvent améliorer leur productivité de 15 à 25%.
Intégrez des formations spécifiques sur l'utilisation de votre système de gestion d'entrepôt (WMS). Assurez-vous que tous les employés comprennent comment utiliser efficacement le système pour localiser les produits, enregistrer les mouvements de stock et générer des rapports. Une bonne compréhension du WMS peut réduire les erreurs de saisie de données de 50 à 70%.
N'oubliez pas d'inclure des formations régulières sur la sécurité. Cela devrait couvrir non seulement la manipulation sûre des équipements, mais aussi la reconnaissance et le signalement des risques potentiels dans l'entrepôt. Des sessions de rappel trimestrielles sur la sécurité peuvent réduire les accidents du travail de 20 à 30%.
Encouragez une culture d'amélioration continue au sein de votre équipe. Organisez des sessions régulières de partage des meilleures pratiques où les employés peuvent échanger des idées sur l'amélioration des processus. Cette approche peut non seulement améliorer l'efficacité, mais aussi augmenter l'engagement des employés.